What was once novelty has subtly developed into a remarkably successful method of community building, as evidenced by Lennar’s 3D printed homes, which feel remarkably similar to the early days of the automobile. Wolf Ranch in Georgetown, Texas, has garnered national attention recently—not for its conventional show homes, but rather for its fleet of robotic arms that are layering concrete into sturdy, curved homes.
Lennar’s collaboration with ICON has revolutionized construction logistics, adopting a particularly creative approach that shortened construction schedules while increasing structural integrity. Their Vulcan printers, which combine state-of-the-art robotics and software, work nonstop, producing full-wall systems with remarkable accuracy and remarkably consistent performance.
Project Information | Details |
---|---|
Development Name | Wolf Ranch 3D Printed Homes |
Partners | Lennar Corporation, ICON |
Location | Georgetown, Texas |
Launch Year | 2022 |
Total Homes | 100 |
Starting Price | ~$384,490 |
Home Models | Dyce, Ezra, Rune, Cato, Nye |
Primary Material | 3D Printed Concrete |
Official Website | Lennar 3D Printed Homes |
Lennar and ICON significantly increased construction speeds through strategic alliances and unrelenting on-site innovation. By growing operations from two to eleven machines, they were able to cut print times in half within the first year. Five years ago, this feat would have seemed purely hypothetical, but they achieved the remarkable feat of producing two homes per week by utilizing continuous 24-hour printing schedules.
With large, two- and three-bedroom models starting under $400,000, Lennar’s 3D printed homes are surprisingly inexpensive given the growing shortage of building materials and rising construction costs. With features like solar panel integrations, high thermal mass for energy efficiency, and incredibly durable concrete shells rated to withstand hurricanes and wildfires, each carefully designed home is remarkably suited for Texas life.
Upon entering a Wolf Ranch residence, guests are immediately struck by the wide-wale, textured walls that bear the distinctive mark of layered printing. The houses don’t feel industrial at all; instead, they have curved edges rather than sharp corners, creating visually appealing and peaceful spaces. These homes elegantly meet functional needs while subtly celebrating their method of creation, much like a masterful sculpture.
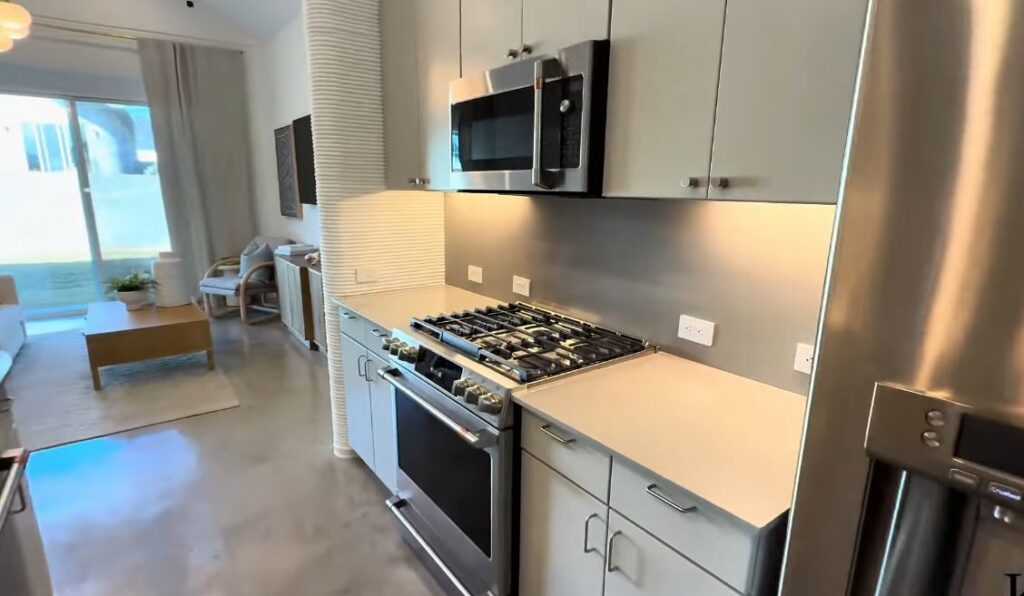
Lennar built homes with solar roofs and thermal efficiency as top priorities, resulting in electric bills as low as $26 per month for homeowners like retiree Holly Feekings. She claims that the construction of the house feels incredibly secure and provides her with a level of peace of mind that she has never found in homes with traditional framing. Feekings describes the printed home’s resilience to wind and fire as “like living inside a modern fortress,” designed with comfort and sustainability in mind.
The high ceilings, cement floors, and sleek lines around the corner particularly appealed to young professionals like Pierre Megie and his girlfriend, whose desires for functional yet fashionable living were well-matched by the architectural choices. Their enthusiasm is indicative of a growing generational shift in which sustainability and usefulness are just as important as aesthetics.
Thanks to the convergence of robotics and digitization, construction innovation has exploded in the last ten years. Lennar’s adoption of this movement was especially audacious since they chose to construct an entire neighborhood rather than specialized showpieces, placing a wager that scale would reveal unanticipated efficiencies. They were correct. Lennar and ICON’s operation significantly exceeded initial estimates by the second year, lowering reliance on manual labor by almost 70% per household.
Working with innovative architectural firms such as BIG-Bjarke Ingels Group, Lennar was able to create homes that are incredibly livable rather than experimental. Instead of just displaying technological prowess, open floor plans, sustainable materials, and adaptable layouts demonstrate a design philosophy that prioritizes human needs.
The low waste output of 3D printing provides an incredibly powerful remedy for climate change. Printed homes produce nearly no extra material, in contrast to traditional builds where drywall debris and scrap lumber are piled high. Lennar’s Wolf Ranch initiative over the past year has shown that when innovation is scaled carefully, sustainability and profitability can coincide remarkably well.
The idea of resilient, energy-efficient homes gained even more appeal during the pandemic, when remote work changed the housing market. The printed homes at Wolf Ranch regularly provide the comfort, security, and reduced operating costs that families were looking for.
Through the incorporation of digital workflows into conventional real estate operations, Lennar successfully prepared its development strategy for the future. Lennar’s printed communities demonstrate how construction can dynamically adapt to changing challenges, while competitors struggle with labor shortages and skyrocketing costs.
Lennar and ICON hope to expand the Wolf Ranch model throughout Texas in the upcoming years, offering even more cost savings and increased efficiency. Every stage of growth will broaden their understanding and improve procedures, much like a software update greatly increases the speed and dependability of an operating system.
Lennar’s strategy provides an especially motivating blueprint for early-stage startups hoping to disrupt an industry: daring experimentation, unrelenting iteration, and scaling only after quality is verified on the ground—not just in labs or slide decks.
Wolf Ranch’s printed houses, which combine automation and creativity, are striking examples of what can be achieved when creativity and willpower come together. Lennar has not only created homes but also made a strong case for the next era of housing, where homes are printed with purpose, optimized for life, and delivered surprisingly quickly, in a sector that has historically been slow to change.